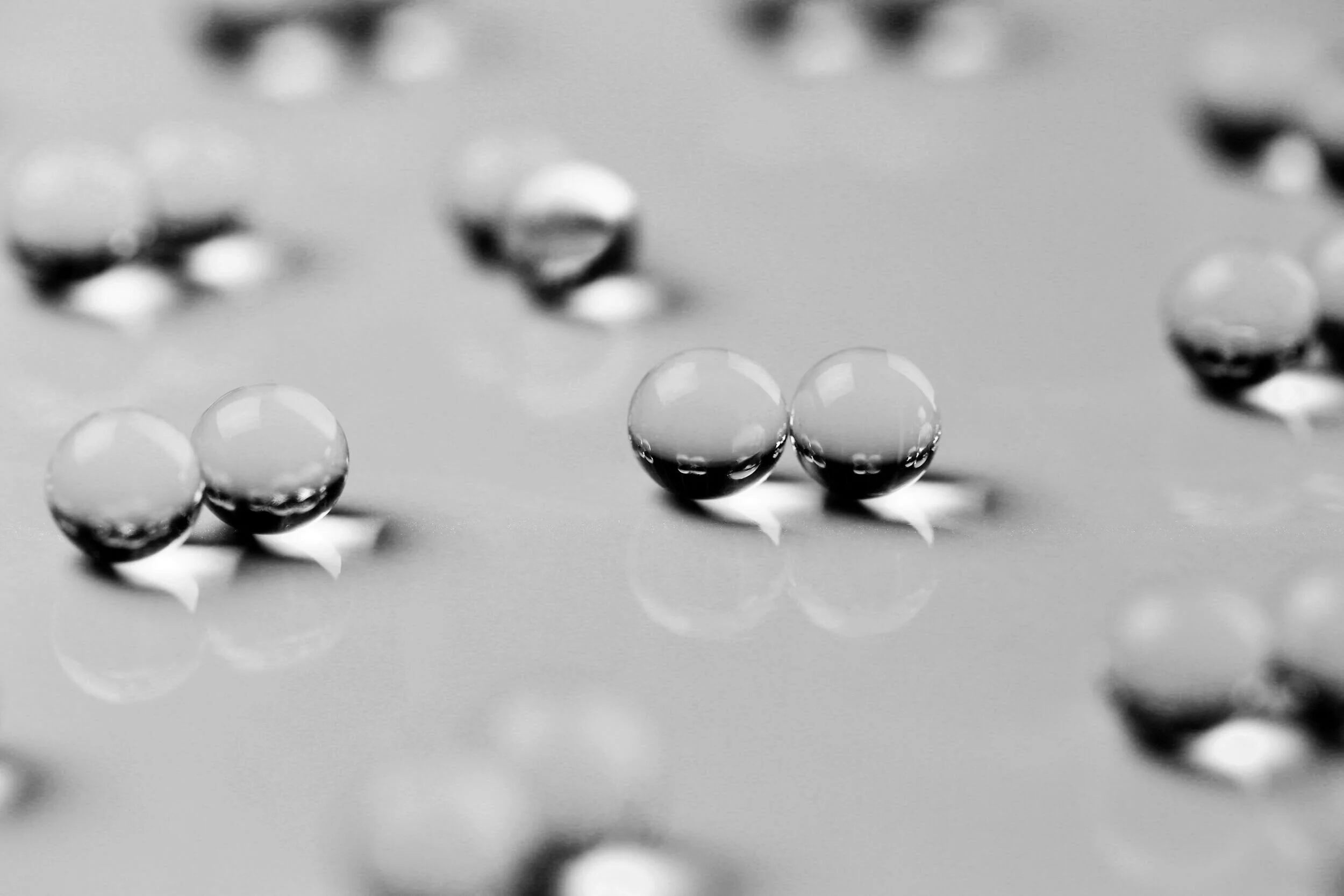
WHAT OUR GAME CHANGING TECHNOLOGY DOES
Our patented Solena Plasma Enhanced Gasification (SPEG) technology produces greener than green hydrogen from any kind of waste – from paper to plastics, tires to textiles. Our technology changes the game, and the world, by solving two global crises: climate change and waste pollution.
Affordable, mass-produced, green hydrogen is the missing link needed to decarbonize the world – with the power and potential to remove or reduce carbon from hard-to-abate sectors like heavy transport, shipping, steel and cement, and reduce the use of natural gas throughout our global economy.
To date, hydrogen has been an industrial captive, but it is now emerging as a commodity that can be traded, opening capital market access, and unleashing tremendous growth.

HOW IT WORKS
SGH2’s unique gasification process uses a plasma-enhanced thermal catalytic conversion process optimized with oxygen-enriched gas. In the gasification island’s catalyst-bed chamber, plasma torches generate such high temperatures (3500º-4000º C), that the waste feedstock disintegrates into its molecular compounds, without combustion ash or toxic fly ash. As the gases exit the catalyst-bed chamber, the molecules bound into a very high quality hydrogen-rich biosyngas free of tar, soot and heavy metals. The syngas then goes through a Pressure Swing Absorber system resulting in hydrogen at 99.9999% purity as required for use in Proton Exchange Membrane fuel cell vehicles. Our process extracts all carbon from the waste feedstock, removes all particulates and acid gases, and produces no toxins or pollution. The end result is high purity hydrogen and a small amount of biogenic carbon dioxide, which is not additive to greenhouse gas emissions.
SPEG TECHNOLOGY EXPLAINED
WHY PLASMA
Plasma technology is based on a principle of physics. When energy is applied, matter changes its state: solids become liquids, liquids become gas. With more energy applied, gas becomes ionized and turns into an energy rich plasma state, the fourth state of matter. A plasma torch produces a direct flow of plasma that reaches temperatures between 3500º and 4000º C. When that flow comes into contact with solid materials like plastic and metals, it changes important properties of that solid. Using a plasma torch, combined with 95% oxygen enriched air, our process produces a high quality syngas without any of the toxic byproducts produced by other gasification companies.
SGH2 PLASMA TORCH
WHY HYDROGEN?
Hyundai’s Hydrogen Guidebook provides basic education about the use of H2 in transportation. Click here to watch all four installments.
HOW IT COMPARES
Ours is greener than green hydrogen.
Lawrence Berkeley National Lab has found that for every ton of hydrogen produced, our process displaces 23 to 31 tons of carbon dioxide. That’s 13 to 19 tons more carbon dioxide avoided than other green hydrogen production processes, which rely on electrolysis from renewable energy.
Traditional green hydrogen made from electrolysis is very expensive to produce and requires tremendous amounts of renewable power, which is intermittent, and water, which is a scarce global resource. Unlike other green hydrogen, our greener than green hydrogen does not require a high electrical energy load. Electrolysis requires 62 KWh to produce 1 kg of hydrogen from 8 gallons of deionized water.
Blue, gray and brown hydrogen producers either use fossil fuels (natural gas or coal), or low temperature gasification (<2000º C) to produce dirty syngas with low hydrogen and toxic tars.
OUR HYDROGEN: MORE CARBON REDUCTIONS, LESS COST
Our greener than green hydrogen is 5 to 7 times cheaper than green hydrogen, and cost competitive with the dirtiest hydrogen.
Our production costs (based on current US costs) are projected to be US$2 per kg of green hydrogen. Brown hydrogen produced from cheap coal in India costs US$2 per kg.
Blue hydrogen — produced from natural gas paired with carbon capture and storage — costs between US$5 to 7 per kg in the US, and $7 to 11 in Europe and Australia.
Green hydrogen produced through electrolysis using renewable power costs US$10 to 15 per kg, depending on availability.
Gray hydrogen produced with cheap, fracked natural gas costs US$2 per kg in the US, while in Europe, Australia and Asia it costs US$5 to 6 per kg due to higher natural gas prices.
Traditional green hydrogen (electrolysis) plants are expensive, have limited capacity, and take a long time to build if they are using new renewable sources like offshore wind.
Our stacked modular design is built for rapid scale and linear distributed expansion, at lower capital costs, and on a fraction of the land required for large scale solar and wind farms. All engineering and construction is standardized and quality assured, performed in collaboration with the largest engineering, procuring and construction companies in the world such as Fluor Group.
Unlike other green hydrogen production from electrolysis with intermittent renewable energy like wind or solar, the SPEG process operates on a year-round base load capacity, and therefore can produce hydrogen at scale more reliably.
Not all hydrogens are created equal. Today gray and brown hydrogen dominate the world hydrogen market, with high greenhouse gas emissions.
Today nearly 99% of the 70 million tons of hydrogen produced each year is gray hydrogen (70%) made from natural gas and brown hydrogen (30%) made from coal gasification. Together, they produce more than the combined greenhouse gas emissions of Britain and Indonesia (Source: IEA)
Our technology changes the game.
A new report from Bloomberg New Energy Finance forecasts the growing global market for green hydrogen, with costs dropping to $US2/kg by 2030 in India and Western Europe. SGH2 is delivering greener than green hydrogen at that price today.
We are the only company in the world producing the greenest hydrogen at scale that is cost competitive with the cheapest carbon-intensive hydrogen made from fossil fuels.
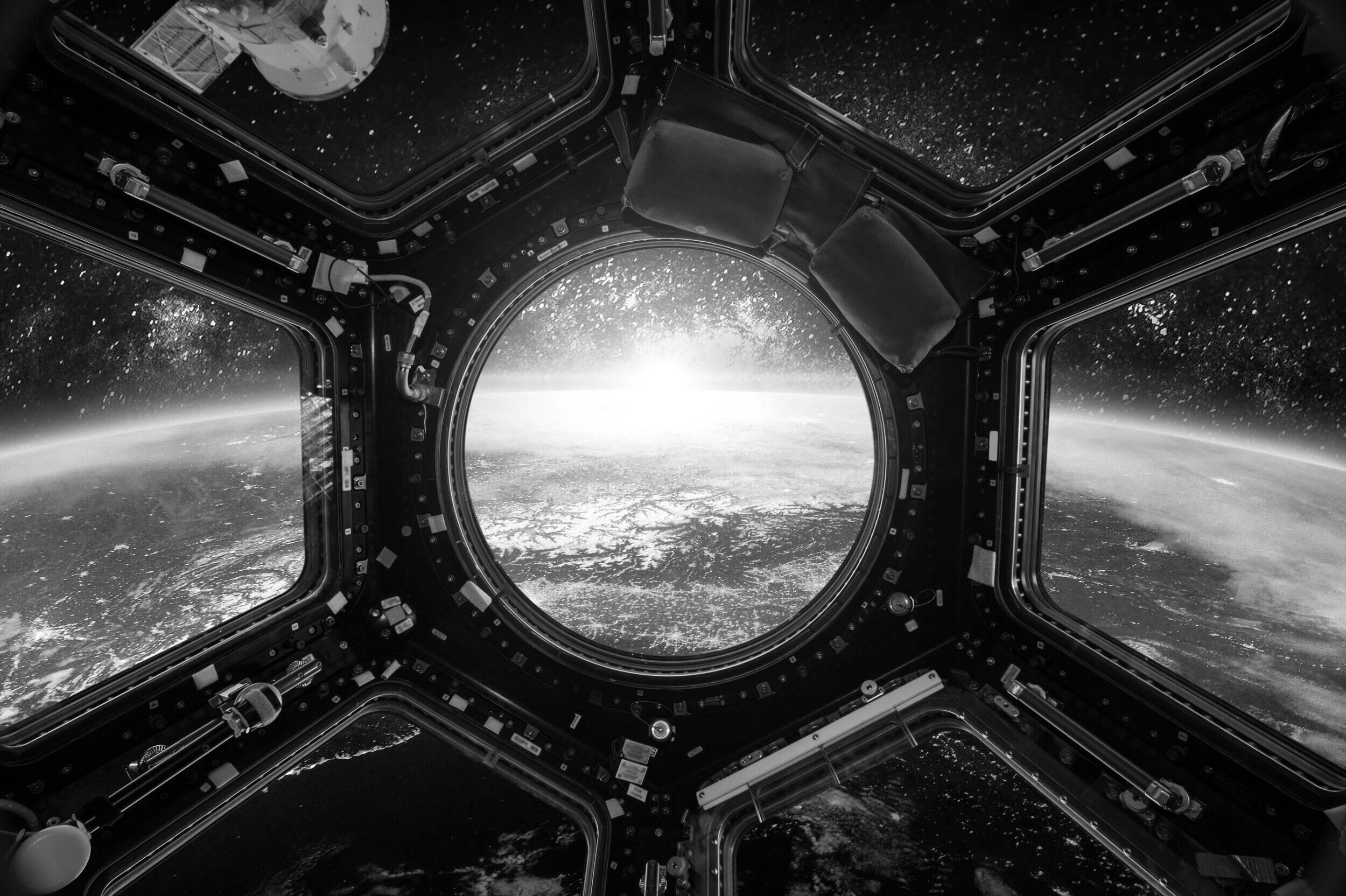
THIS IS ROCKET SCIENCE
Our technology was invented by NASA scientist Dr. Salvador Camacho, “the father of plasma technology,” and Dr. Robert T. Do, a biophysicist, medical doctor and entrepreneur. Dr. Camacho developed the high-temperature plasma torch to test heat shields at NASA. Without his invention, there would have been no way to guarantee the safe re-entry of NASA astronauts into Earth’s atmosphere.
Dr. Do has deep knowledge, experience and expertise in science (Masters in Biophysics, MD from Georgetown University), and spent his early career working around the world on public health, environmental and energy issues.
Dr. Do and Dr. Camacho founded Global Plasma Systems (Solena Group’s precursor), driven initially by the urgent need to safely dispose of medical waste.
While Dr. Camacho’s plasma torch was adopted for industrial use by steel, automotive and other sectors, Dr. Do and Camacho tested new technologies using the plasma torch to solve critical energy and waste issues under the umbrella company Solena Group (SG).
As CEO, Dr. Do has led the growth of Solena Group into a multinational company. He has worked with airlines, waste management companies, government agencies and municipalities around the world including in the United States, United Kingdom, Turkey, Russia, Ukraine, Germany, Sweden, Norway, Denmark, Finland, France, Italy, Spain, Portugal, Indonesia, Malaysia, China, Hong Kong, Singapore, Thailand, Brazil and Mexico. He is lead author and inventor of the current SPGV technologies patents. Solena has licensed its SPEG technology for the production of green hydrogen exclusively to SGH2 Energy Global LLC.
EXPERT VALIDATION
Our technology has been vetted and validated, technically and financially, by leading global institutions including US Export-Import Bank, Barclays and Deutsche Bank and the Fluor Group. One of the world’s largest reinsurers is providing performance output guarantee.
Our technology is time-tested with a proven track record.
Our technology was successfully demonstrated at a full-size project in Pennsylvania and at a plasma torch testing facility in the Czech Republic. The Pennsylvania plant, now dismantled after 7 years of testing, was of similar size and capacity to our commercial plant at Lancaster.
British Airways conducted a yearlong technical and financial feasibility study of our technology, and signed a $600 million contract contingent on a benchmark oil price. The deal was canceled when world oil prices crashed in 2014.
“Hydrogen is the emerging solution for hard-to-decarbonize sectors like the cement industry. SGH2’s solution — to produce green hydrogen and bio-syngas from the gasification of biomass and biogenic waste using its SPEG process — can be a cost competitive solution to provide the high quality heat required in our industry, and replace or reduce the usage of coal and coke.”
— Lawrie Evans, Technical Expert & Director, LafargeHolcim, World’s largest cement company
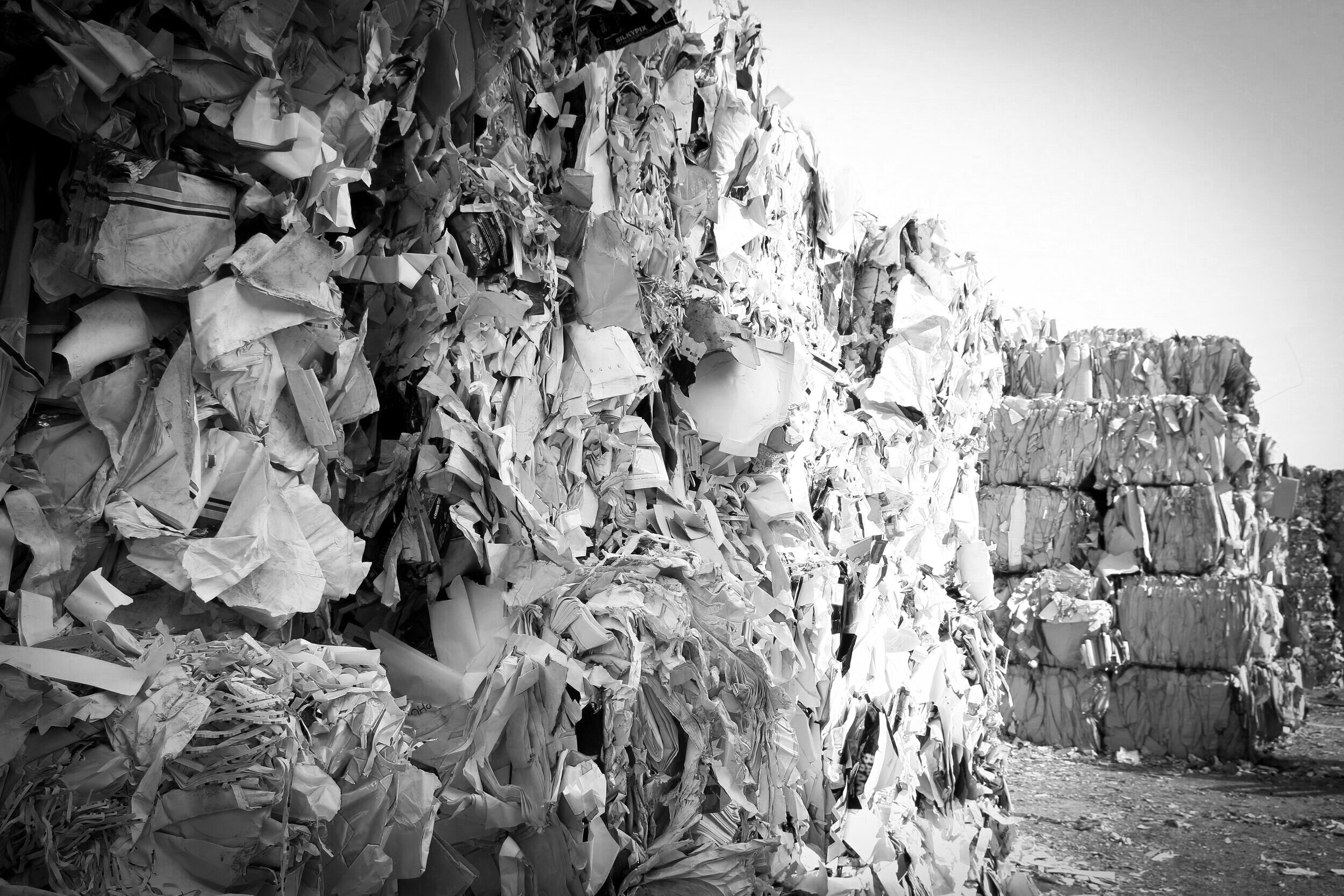