
LANCASTER
SGH2 energy is launching the world’s largest carbon-negative hydrogen facility in partnership with the City of Lancaster, California.
The Lancaster facility will have the capacity to produce 12,000 kg of green hydrogen per day. Operating 24/7, 8000 hours a year, it will generate 3.8 million kg (3800 tons) of green hydrogen per year.
That's nearly three times larger than any other green hydrogen facility — built, under construction or in development within the decade. All other green hydrogen plants produce a much more expensive hydrogen through electrolysis of water using large amounts of intermittent renewable energy.
The Lancaster plant will process 40,000 tons of waste annually. Allan Copany will supply guaranteed feedstock of mixed paper waste, saving between $50 to $75 per ton annually in landfilling and landfill space costs.
The largest owners and operators of hydrogen refueling stations in California signed 10-year off-take agreements with SGH2, guaranteeing the purchase of 100% green hydrogen for this project.
An Atlantic Council report finds that if the SGH2 Energy Lancaster plant can meet its cost and production targets, waste gasification technology could become a critical piece of the U.S. hydrogen economy.
“As the world, and our city, cope with the coronavirus crisis, we are looking for ways to ensure a better future. We know a circular economy with renewable energy is the path, and we have positioned ourselves to be the alternative energy capital of the world. That’s why our partnership with SGH2 is so important. This is game-changing technology. It not only solves our air quality and climate challenges by producing pollution-free hydrogen. It also solves our plastics and waste problem by turning it into green hydrogen, and does it cleaner and at costs far lower than any other green hydrogen producers.”
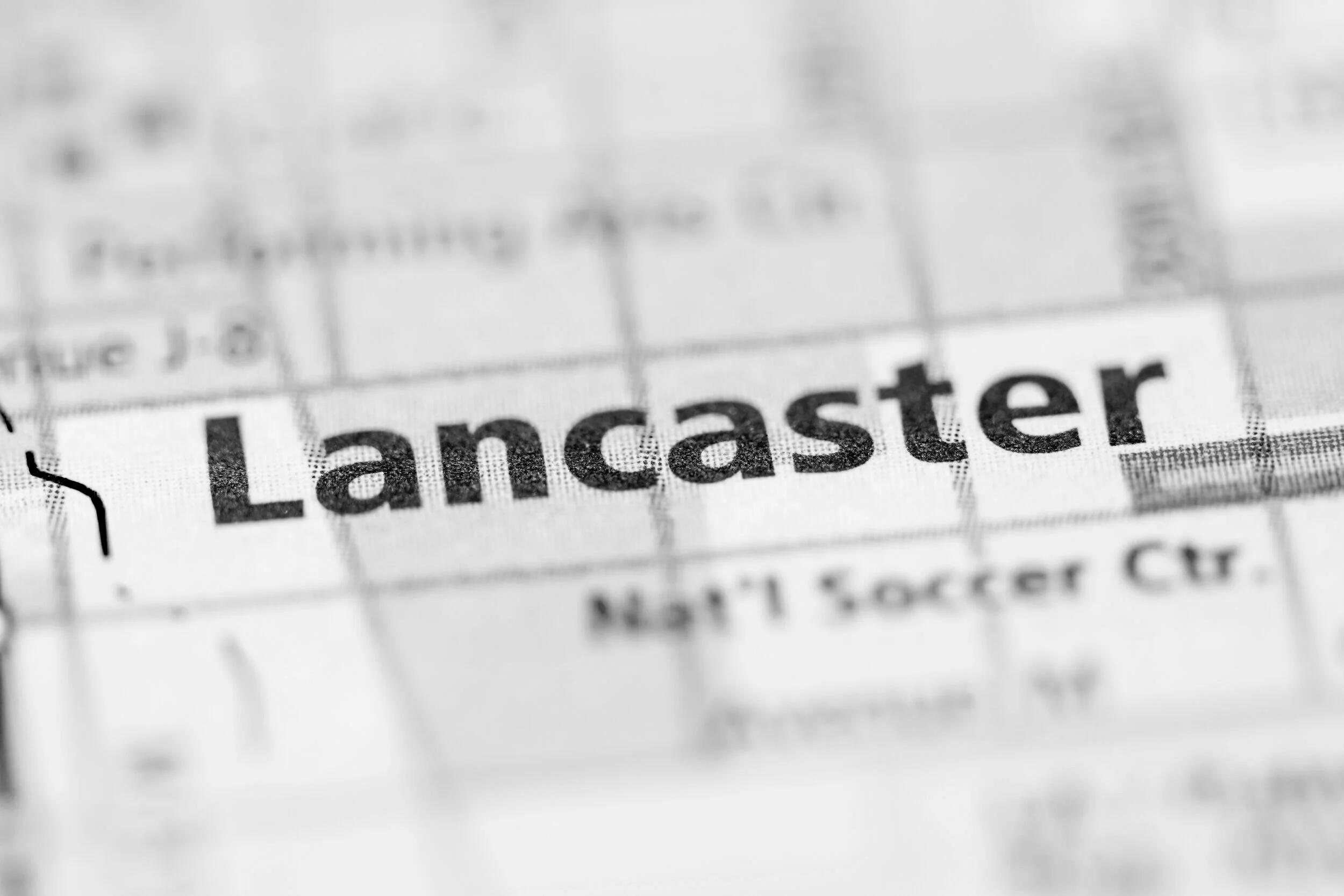
SGH2 Lancaster is meeting the gold standard for production facilties.
A consortium of leading companies and top institutions have joined with SGH2 and the City of Lancaster to develop and implement the project including: Fluor, Lawrence Berkeley National Lab, ABB, Integrity Engineers and Constructors, Munich RE, and Stork.
Fluor Group, a leading global engineering, procurement, construction and maintenance company, which has best-in-class experience in building hydrogen from gasification plants, will provide the front-end engineering and design. Fluor Group is also providing a Complete Technology Integration Performance guarantees for the project, including Solena’s SPEG, Honeywell/UOPs PSA and Jenbacher’s Power Block.
Munich Re, the world’s largest reinsurer, will underwrite SGH2 Complete Plant Output Guarantee to cover all revenues shortfall should there be any underperformance issues at the Lancaster Plant. Munich Re will also underwrite SGH2’s Complete Performance Guarantee for its SPEG system with a full repair and replacement for any design/engineering/equipment issues with the SGH2 Gasifier performance.
Two world-leading engineering procurement construction management (EPCm) companies will be tendering to provide the turnkey lump sum EPCm contract for the Lancaster project, guaranteeing total costs and the construction schedule.
GLOBAL EXPANSION
SGH2 is in negotiations to launch more projects around the world.
SGH2 is in negotiations to launch projects of similar modular size to Lancaster in France, Italy, Netherlands, Belgium, Germany, Saudi Arabia, Greece, Japan, South Korea, Poland, Turkey, Brazil and Australia. SGH2’s stacked modular design is built for rapid scale and linear distributed expansion, at lower capital costs and does not require large land space as do solar and wind based projects or unique weather conditions.
TRACK RECORD
Our technology is time tested with a proven track record.
Our technology has been vetted and validated, technically and financially, by leading global institutions including US Export-Import Bank, Barclays and Deutsche Bank and the Fluor Group.
Our patented technology is tested and proven.
Our technology was successfully demonstrated at a full-size project in Pennsylvania and at a plasma torch testing facility in the Czech Republic. The Pennsylvania plant, now dismantled after 7 years of testing, was of similar size and capacity to our commercial plant at Lancaster.
British Airways conducted a yearlong technical and financial feasibility study of our technology, and signed a $600 million contract contingent on a benchmark oil price. The deal was canceled when world oil prices crashed in 2014.
“We have great expertise in building large scale hydrogen production plants from the gasification of coal and petroleum residues, which are carbon dioxide emission intensive. However by gasifying renewable feedstocks such as recycled paper waste, SGH2 can produce green hydrogen at scale and at a competitive price at base load production compared to the alternatives with the added benefits of avoiding methane emissions from landfills and needing more landfills.”
— Ravi Revikumar, Fluor Executive Process Director
